FAÇADE STEEL REPAIRS
- Cuono Engineering PLLC
- Sep 1, 2022
- 3 min read
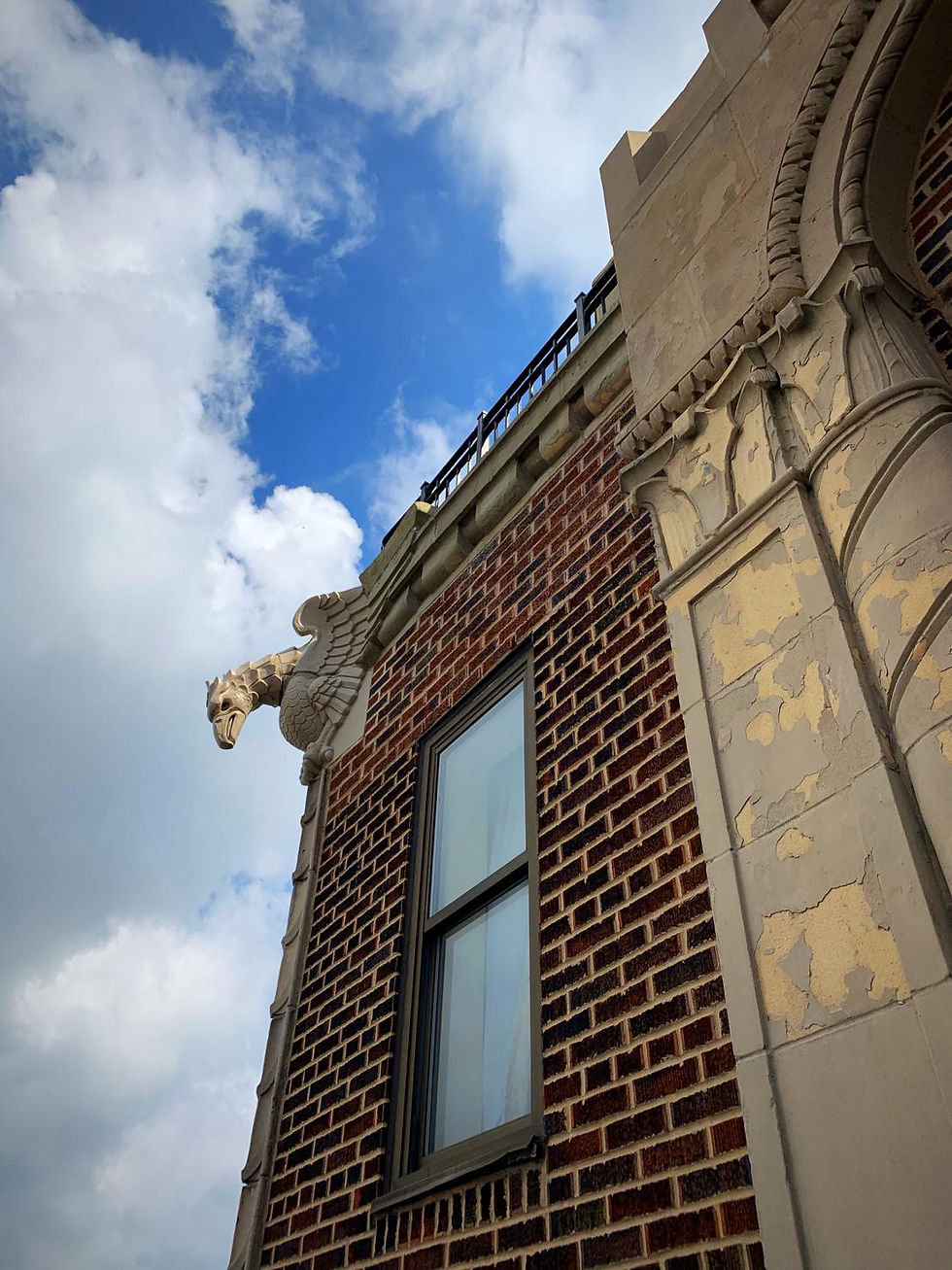
From the 1870s to the 1930s, New York City and surrounding cities boomed with the construction of multi-story “steel skeleton” structures. Many of these buildings were ornately decorated in terra-cotta, limestone, and other decorative masonry and were lauded as architectural marvels. This ornate and rich craftsmanship is supported by a robust framing system of steel columns and beams embedded within façade walls and which typically haven’t seen the light of day since they were constructed over 100 years ago.
Building methods during this boom era were constantly evolving as with every new structure erected, innovation and previous experience were continually tested and improved upon. It was known that steel corrodes when exposed to moisture and oxygen, however, modern waterproofing membranes had yet to be invented. Building envelope systems of the time assumed that the multi-wythe masonry facades would serve as a sufficient protective barrier for the structural steel skeleton from the harsh exterior elements. In typical rain scenarios, the outer layer of brick would absorb the majority of the moisture while keeping the inner layers of brick and steel dry. However, over the course of a building’s life, weak points develop in the wall where water can penetrate the “protective” barrier, reach the steel, and cause the steel to corrode and deteriorate. These deficiencies, such as cracks, deteriorating mortar joints, and deteriorating window lintels, and sills, can be caused by natural aging of the material, hard wind-driven rain, freeze-thaw cycles, and settlement.
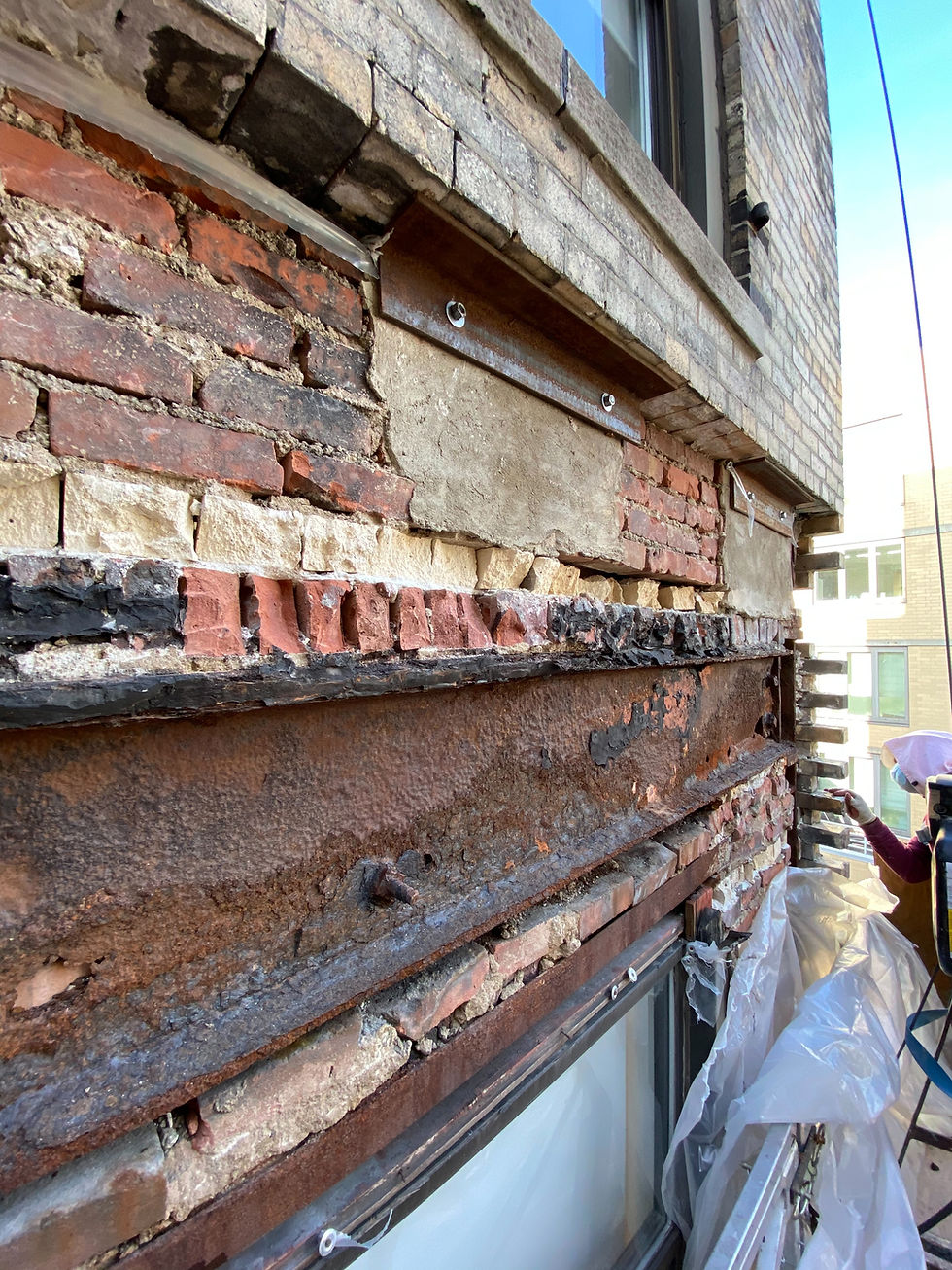
Due to the fact that these embedded structural members are not visible, they may be slowly deteriorating for years or decades before their deficiency is discovered. Sometimes, newly exposed steel deterioration is so advanced that emergency shoring is necessary to provide alternative means of support until repairs can be made.

Steel will begin to rust when it is exposed to moisture and oxygen. Minor surface rust does not contribute to loss of strength because the chemical deterioration has not yet penetrated beyond the surface layer of the steel member. However, if the surface of the steel remains in contact with moisture and oxygen, the resulting corrosion will continue to penetrate deeper into the steel material and cause a type of deterioration called delamination.
Delamination of the steel is where the outermost layers of the steel material begin to separate from the base material in layers. In severe cases, delaminated steel material can be removed by hand, as seen in the video below.
These kinds of material loss (section loss) contribute to loss of strength. If a deteriorated steel member is encountered in the field, it is recommended for a structural engineer to visit the building, survey the existing conditions, analyze potential section loss of the existing member, and design a repair program.
Typically, deteriorated façade steel is repaired by welding a new steel section to the exposed web of the existing beam. “C” shaped steel members, or channels, are selected by the structural engineer to provide additional strength to the existing beam equivalent to that which was lost to corrosion. Historic steel contained higher levels of carbon than today’s steel, and high carbon materials such as cast iron cannot be welded to. Therefore, for historic steel, performing a weldability test on the existing material is essential to determining if a welded reinforcement program is feasible.
As previously mentioned, not all embedded façade steel is deteriorated and in need of repair. So, how can a building owner tell if their building steel needs repair without opening probes at every single beam and column location? The good news is that there are signs that a façade inspector can look for when surveying a building façade. Steel expands as it corrodes, and this expanding material creates internal pressures on the surrounding masonry which can cause masonry units to crack or bulge. Large areas of cracking or bulging masonry may be symptomatic of deteriorating steel within the wall. Parapets, protruding balconies, decorative terra-cotta features, and building corners are vulnerable façade elements that are located at points of the building where wind blows at higher forces and can exacerbate poor façade conditions. These symptoms and vulnerable locations should be continuously monitored and periodically probed so that deterioration of the structural steel is identified and addressed. When and where structural repairs are completed, a façade engineer or architect is typically engaged to provide waterproofing details that will protect the steel from future corrosion.
Commenti